Editor’s note: This is the fourth in a series of four blog posts on quality risk management. Follow for these and more upcoming regulatory updates in 2023.
Let it go
Once I have a complete map of a process in front of me, I feel assured that I can articulate a list of recommendations. I hate making suggestions when I don’t have a good frame built to economize possible enhancements, because they almost feel like random ”shots in the dark” that may add to the problem instead of take away from it.
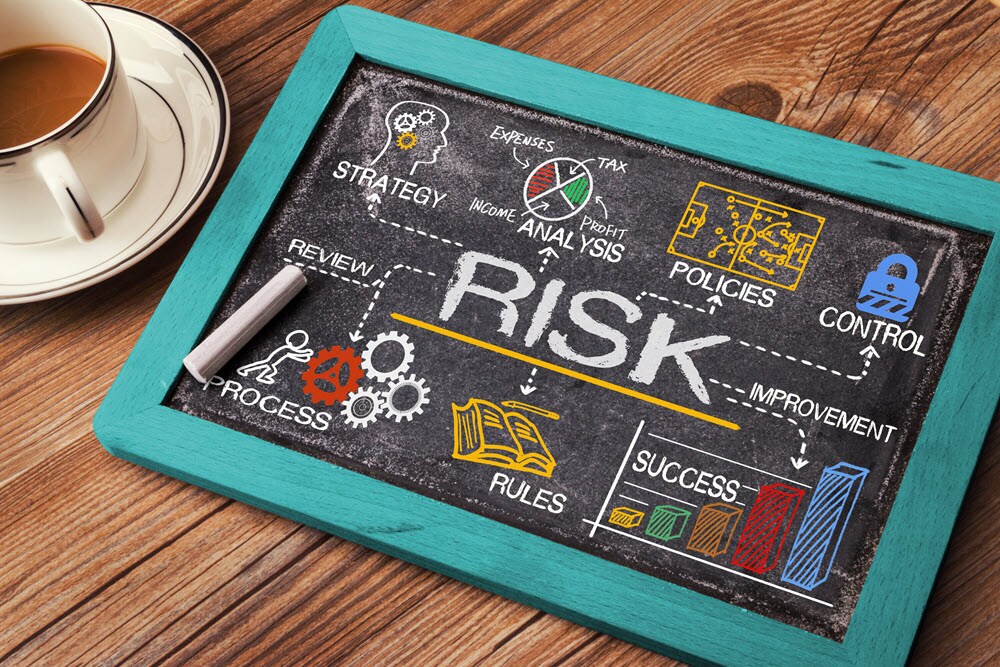
On the other hand, once I have a complete map, I can start to dig so far into the finer details that the amount of control is anxiety inducing.
So, over the course of my career, I have attempted to temper my enthusiasm for enacting change on large scales and try to recommend to others (and remind myself) that sometimes it’s just better to let a few things go.
QRM changes worth noting
By far, the largest change to the Quality Risk Management (QRM) guidance is within the methodology and integration sections. Emphasis is placed on leveling the formality of a risk and making decisions for actions required based on that level.
It is stated and understood that regulatory bodies are aware that maintaining quality takes a lot of resources. I argue that this guidance is an important tool for companies to adopt in all their procedures so that they can reduce those resource requirements.
“As outlined in the introduction, appropriate use of quality risk management does not obviate industry’s obligation to comply with regulatory requirements. However, effective quality risk management can facilitate better and more informed decisions, can provide regulators with greater assurance of a company’s ability to deal with potential risks, and might affect the extent and level of direct regulatory oversight. In addition, quality risk management can facilitate better use of resources by all parties.”1
I encourage anyone in quality leadership who is facing large amounts of resource investment in quality activities to reflect on the clarifications in these sections. While adopting a risk-assessment-based system could seem like adding more resources to an already heavy burden, a structured QRM will pay for itself.
Don’t forget the feedback
A feedback program is a necessary component for continuous improvement, however, I found that feedback systems designed for that sole purpose are often left to maintain themselves and can fall into disuse.
To mitigate the possibility for disuse, I would try to fit feedback systems in places where I was more assured they would be maintained. As an example, adding QRM scoring to deviation logs could be a helpful enhancement and feedback mechanism that allows for cross analysis with repeated errors. It could also trigger an investigative loop that would hopefully result in a reduction of repeated errors and demonstrate that the system is within control.
Deviation Reference: Description | Captured in QRM | QRM score | Impact to product | Impact to department | QRM change |
123-1234: Missed vial caused system shutdown | Yes | Low | Low – analysis was rerun | Medium – Right First Time metrics | None |
123-1566: Improper use of manual integration to meet sample criteria | Yes | Medium | High – product stability study deviation | High – requires change event | Score changed from medium to high for critical integration change |
In most quality systems, the deviation log is highly maintained, so it proved an effective way in my past to capture a continuous improvement effort around QRM. There could be other systems in an organization that prove more appropriate. Perhaps there is a regular audit program run by the quality unit that could include QRM scoring for any captured observations in addition to — or instead of — the deviation log.
My overall goal was to keep the feedback in a system that was actively maintained so it does not introduce an entirely new system that could fall into disuse.
High-risk activity: manual changes
In this fourth blog in the series on risk management, the feature focus is on the review-by-exception tools and modifying views in Thermo Scientific Chromeleon Chromatography Data System (CDS).
The topic of manual changes in industry can get heated. Algorithms and computers are supposed to offer a non-biased way of providing results but are still fallible human creations that can be influenced by the slightest mathematical variation in data. Humans, by contrast, are visual creatures first and rely on data interpretation made against the whole picture.
Chromeleon CDS offers several visual-based tools to both assist the fair use of — and allow for the review of — human-directed manual changes. First and foremost is the ability to unify how data is viewed with ability to save views.
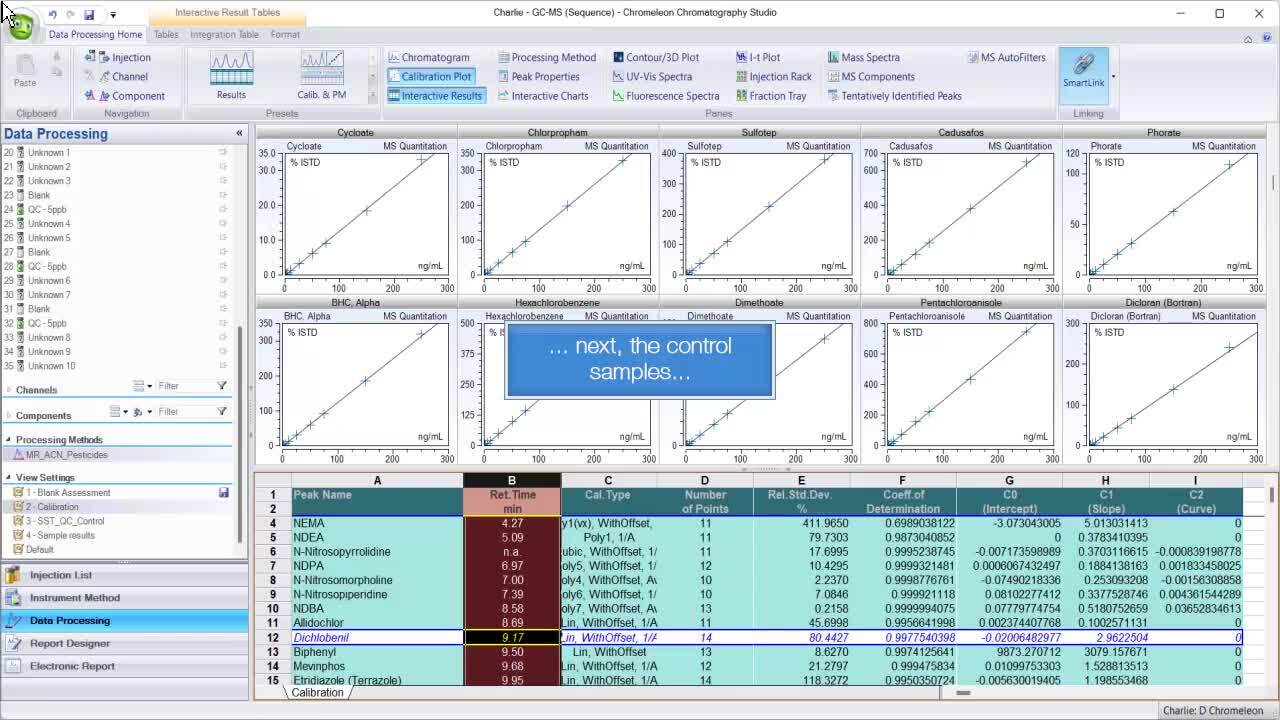
Being able to compare method changes side by side is helpful for understanding the history and maintaining control over critical method parameters.
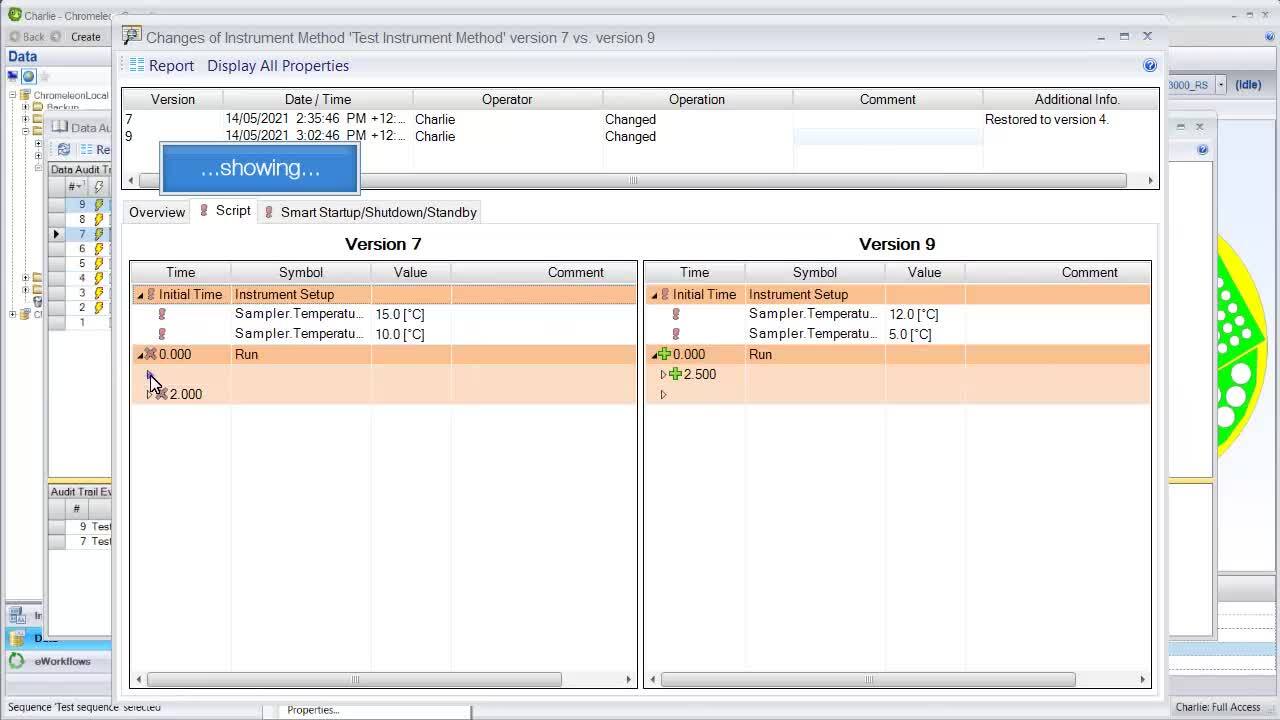
Often the hottest topic is the ability to track human-made changes to peak integration. With the view option to always have the autogenerated version compared with the manual one, a simple walk through the samples will reveal which ones have been edited when the view changes.
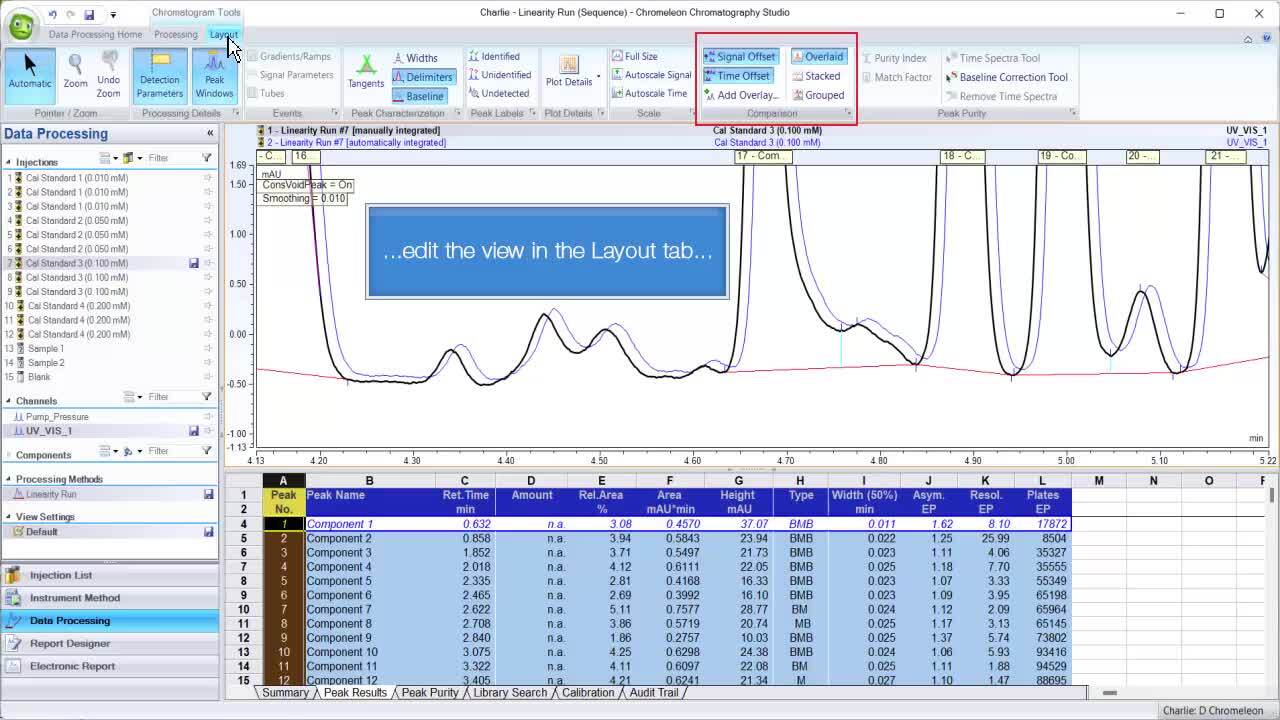
Additional resources
- Chromeleon CDS Software – Built for Compliance
- Whitepaper – Are you audit ready? Ensuring trustworthy data
- Blog post part 1: Quality Risk Management: Know the Risks
- Blog post part 2: Quality Risk Management: Defining Responsibilities
- Blog post part 3: Quality Risk Management: Don’t Discard Standard Lab Practices
For technical application development support, Thermo Fisher Scientific also has a complete service offering. Services and support plans include product updates, technical support, additional resources, and training.
Take-home message
In closing this series on quality risk management, I hope that some of the thoughts I’ve shared have been impactful and worthwhile. Even though quality can sometimes be dismissed as a more ”elementary” science, one cannot overstate the fact that quality has a critical impact on patients.
I am very thankful that I had the opportunity to build a strong foundation in a quality organization early in my career and I encourage those interested in drug development to spend some of their career in quality.
Is there is a tool you’ve implemented in quality risk management that has saved your organization a lot of time? Is there something you wish you had started doing sooner?
Citations
1 ICH Q9(R1), section 6. ICH resources page. https://database.ich.org/sites/default/files/ICH_Q9%28R1%29_Guideline_Step4_2023_0126_0.pdf. Accessed July 7, 2023.